 |
| |  |
 |
 |
|
|
CARBURISING
Carburising is a process where the steel is heated in a furnace. By means of a carbonaceous medium (gas or salts) the outside layer of a carbon poor component is enriched with carbon by means of carbon diffusion. The increase of carbon content causes the material to harden. The result is a hard and wear resistant surface with a tough core.
The temperature is relatively high since in austenite, the high temperature modification of iron, carbon is more soluble than in ferrite, the low temperature modification of iIron. In carbonitriding besides carbon, nitrogen is also disolved in the material surface. The carbonitriding layer is thinner than a carbonised layer.
Carburising in a gas atmosphere, unloading of the furnace.
Properties
The fully treated product has a hard surface (under compression) and a very tough inner part.
Carburising causes the wear resistance of the surface to increase, the fatigue strength is improved as well as the toughness of the material. The strength and toughness increase are dependent on the steel alloy composition.
Cross section of a carbonised surface.
The thickness of the carburised layer is depending on the carburising temperature and time as well as the carbon potential of the steel.
The depth of hardening is defined as the depth where the hardness is 550HV. The structure is then 50% martensite and 50% pearlite.
A usual depth of hardening is:
Carbon penetration curves during carburising.
0,1 to 3,0 mm during carburising.
0,05 to 0,7 mm during carbonitriding.
Schematically after time t (curve a) and 4t (curve b).
|
|
Cross section of a carburised and hardened axle;
Enlargement 2x.
Hardness: 700 - 950 HV;
Hardening depth: 0.1 - 3.0 mm after carburising, 0.05 - 0.7 mm after carbonitriding at temperature of: maximum 175 - 200 °C.
Quality of the surface: As untreated steel
Hardness: Increases
Toughness: Decreases as a result of notch formation in the layer.
Impact strength: Good
Tensile strength: increases
Corrosion resistance: Similar to the base material, unalloyed steel therefore. |
Process characteristics
Substrate
Carburising can be applied on unalloyed steel, low alloyed steel and nitrided steel. The selected of steel quality is on the one hand determined by the desired tensile strength of the core material (core consistency) and on the other side by the demands which are made in using the component. C10 and C15 are used (unalloyed steels with 0.1% to 0.15% carbon) for wear resistant components of small dimensions and low strength: office machines, bolts, barrels, pins and bicycle collars.
15 Cr 3 (low alloyed steel with 0.15% carbon and 0.75% chromium) is used when a higher strength is desired, as in the case of gudgeon-pins, chain bracelets and rulers.
Cr-Mo or Cr-Mn-steel; steel with up to 0.45% c and 1% of the alloy elements is used for parts which are subject to tension, compression or bending. Examples are cog wheels, axles and bolts with a diameter of maximum 60 mm.
Cr-Ni-Mo-steel; steel with up to 0.4% C and up to 4% alloy elements are used where additional shock resistance is required.
Process characteristics
Carburising is a process where the steel piece is heated to the austenite range (850 up to 950 °C) when the surface takes up carbon up to 1%. Carburising can be carried out as:
- gas carburising
- salt bath carburising
- plasma carburising
The carbon containing gas decomposes at the surface and supplies carbon to steel. Carbon diffuses into the material. The diffusion rate depends on the temperature, the carbon concentration in the steel and the carbon potential. During carbonitriding both carbon and nitrogen diffuse carbon into the material.
Hardening depth: 0.1- 3.0 mm at carburising, 0.05 - 0.7 mm at carbonitriding
Formation rate of the layer: 0.02 - 0.035 mm per hour. Process temperature: 800 980 °C.
Dimensional deviation: .2% increase of the dimension.
Shape stability: selective increase of angle points. Adherence: good, because the layer is integrated in the matrix material.
Pre - processing
The pieces should be clean, i.e. free of an oxide layer, dirt, cleaning agents etc. Further requirements of the work pieces is that they:
- have some excess dimensions in order to compensate for changes in shape
- are free from stress as a result of machining.
During pre-treatment some dimensional increase must be taken into account. Carburising causes a small change in tolerances.
Carburising
Introduction of the component into a furnace with a carbon containing atmosphere. The layer thickness depends on the process time, 0.1 to 3.0 mm.
In case of carbonitriding the layer is thinner, 50 up to 700 µm.
Structure of the carburised layer.
After - treatment:
After the diffusion treatment the work piece is hardened. Hardening depth is up the point where hardness is 550 HV. The hardening depth normally is approximately 40 to 60% of the layer thickness.
|
|
Hardheid kern = Hardness of the core
Hardingsdiepte = Hardness depth
Totale laagdikte = Total Layer thickness
Diepte onder het oppervlak = Distance under the surface
Hardness distribution under the surface. |
Hardening can take place directly, starting at the carburising temperature (direct hardening) or in two steps: first cooling down to room temperature and then again warming up to the hardening temperature (indirect hardening).
|
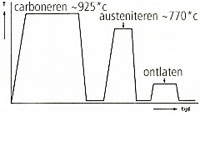 |
Carburising and direct hardening of carburised steel. |
Carburising and indirect hardening of carburised steel. |
Advantages and disadvantages
Advantages:
Good combination of hard layer and tough core. Good adherence by diffusion.
Disadvantages:
dimensional deviations by the high temperature process and the hardening treatment. Selective increase of the angle points; expensive machining. The dimension of the work piece is limited to the size which fits the hardening furnace.
Costs
The costs amount to € 1 to € 3.5 per kilogramme weight of the work piece.
Application
Carburised components are applied in cases where hardness, wear resistance and toughness of the surface as well as toughness of the core material are required. Not too heavily charged components of low carbon steel in the machine industry. Examples are machine parts, such as axles, bolts and gears.
The maximum application temperature of the carburised piece is up to 175 - 200 °C, at higher temperatures the properties of the layer quickly decrease, because the outer martensitic layer becomes soft.
Drive shaft, quenched after carburising to obtain the correct hardening.
Carburising – Conditions
The material needs hardening after carburising. During carburising small dimensional changes may occur. This can be tackled by slight over dimensioning. Ion order to reach the desired dimensions, part of the carburised layer can be removed by machining.
| 
|
| 
|

|

|
|