 |
| |  |
 |
 |
|
|
NICKEL PLATING
1. Introduction
Nickel electroplate is deposited onto products by placing them in an aqueous solution of nickel salts, connected as the cathode. Nickel anodes are used to complete the circuit, these are dissolved during the plating process to maintain the overall nickel metal concentration in the solution. Organic additions are added to obtain levelled deposits as well as bright decorative coatings.
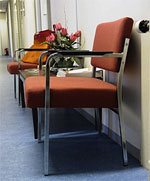
Nickel and chromium plated chair frame
2. Properties
Nickel layers are decorative, corrosion and wear resistant. Depending on the organic additions the deposit can exhibit hardness values between 150 and 500 HV. The metal layer may have varying levels of internal stress and ductility. Bright nickel looks yellowish in daylight and tarnishes easily. For this reason it is commonly covered with a top layer, e.g. chrome or gold.
3. Substrates
Nickel layers can be applied to all commonly used pure metals and alloys. Substrates include: - unalloyed and low alloyed steel, copper and copper alloys, brass, zinc and aluminium alloys as well as certain plastics.
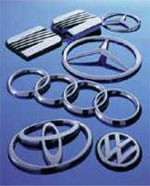 |
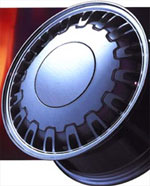 |
Nickel and chromium plated plastic parts |
Nickel plated plastic wheel cap |
4. Process characteristics
The nickel plating bath can be manipulated to provide a wide range deposit properties. The commonly used baths produce a number of different types of finish.
- Bright nickel is used to provide a top coat, sometimes the final finish, more often the final undercoat for decorative chromium.
The plating bath contains organic additives to provide a bright and level deposit.
- Dull or matte nickel has a better corrosion resistant and has better mechanical properties. It is deposited as a thicker underlayer below bright nickel and provides a robust substrate for products used in severe environments, e.g. external applications, on motor vehicles and for components subject to salt water.
- Satin nickel finishes are produced by adding an emulsifying agent to the nickel bath so that the surface is pock marked. A final chromium coat may be applied.
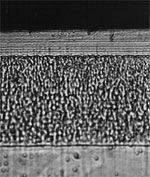 | |
Cross section of a duplex nickel electroplate. |
The first layer on the steel substrate is a nickel underlayer. This nickel has good covering properties. The second layer has a lamellar structure giving good reflectivity and brightness. There is an outermost thin layer of chromium (0.2 microns).
|
|
The surface structure of dull nickel |
The surface structure of satin nickel.
Additions to the electroplating bath cause these surface irregularities.
|
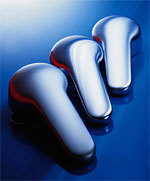 | |
Special matte nickel.
|
Additions to the nickel bath cause a surface structure which reflects light diffusely which gives a very pleasing appearance.
5. Pretreatment prior to nickel plating
The substrate needs to be free of grease, oil, scale and oxide. Generally the following steps are required: -
1. cleaning and degreasing in alkaline water based cleaners
2. rinsing
3. electrolytic degreasing in alkaline water based cleaners
4. Rinsing
5. acid dip pickling in acid based solutions
6. rinsing
7. activation (if required) in specialist solutions
Certain materials such as zinc, stainless steel, aluminium alloys and plastics require special pretreatments prior to nickel plating.
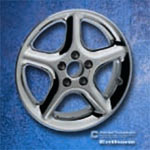 |
|
Nickel plated aluminium hub cap
|
6. Deposition
The components are immersed in a nickel solution and connected to the cathode side of a DC plating cell. Products are usually suspended using specially designed jigs disposed so that an even coating is obtained all round the parts. Large quantities of small parts can be plated in drums or barrels.
For decorative applications thicknesses of 5 to 10µm are common, in duplex systems up to 40 or 50µm deposits are not uncommon, depending on the severity of conditions the product is to withstand. For functional applications much thicker deposits are possible.
After nickel plating the parts are thoroughly rinsed and often plated with chrome.
See ISO 1456; ISO 4525.2; DIN 50960 Teil I; refer also to www.bsi-global.com.
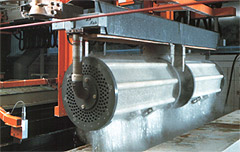 |
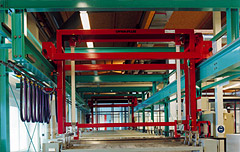 |
On-line barrel plating.
The figure shows the drum above a rinsing bath. After rinsing in clear water the drum is hoist whilst still rotating.
|
Automatic nickel plating line. |
7. Advantages and limitations
Advantages
- attractive looking, decorative layer
- corrosion and wear resistant
- different bath compositions can be used for very differing applications
- can be applied on a wide variety of substrate materials
- often a good underlayer for other surface coatings.
Limitations
- Discolouring of nickel in air necessitates the use of a top layer (chromium). For electronics a final coat of gold may be necessary.
- Nickel may cause allergic reactions
- Layer thickness and structure depend on the current density, as is the case in most electrochemical processes. This limits the shape of objects to be coated.
Cost
Very dependant on the number of process steps and the layer thickness.
| 
|
| 
|

|

|
|