 |
| |  |
 |
 |
|
|
ORGANIC COATING
Organic deposition techniques : wet painting and powder painting
The deposition of organic coatings is a most important technology. They can be applied in many ways, the application techniques depending on the coating material and the material to be coated. A substantial advantage is that for very many product materials there is usually an appropriate organic coating.
The coating can be applied as foil or tape, but also as a powder or suspension/solution.
|
|
A foil is rolled on to a steel plate which has been coated with zinc using electro deposition and on which a glue has then been deposited. |
Foil is often used in the coilcoat industry where the foil is rolled on with a cylinder.
Tape is used for the covering of transport pipes used underground. Special winding machines are used in this case.
Most often organic coatings are applied as powder or suspension.
Powder coatings can be divided into thermohardening and thermoplastic, depending on the binding agent in the powder. Thermoplastic coatings are applied via spinning methods.
Pretreatment
Before application of an organic coating the substrate should be pretreated. The pretreatment depends on the requirements of the coating.
Pretreatment is less challenging for objects which are treated in-house.
It can consist of degreasing, pickling and application of a conversion layer. Also mechanical pretreatment is often used, for instance machining, polishing and brushing. Deburring will improve the appearance of the coating.
For constructional steel, blasting is often used. This can be done in different ways, e.g. pneumatically or shot blasting.
Degreasing and cleaning
Degreasing and cleaning before painting can be done with water - based or organic cleaning agents. The use of organic cleaning or degreasing agents such as trichloethane, perchloethylene and benzene is restricted for health reasons. The majority of companies are now cleaning with water-based agents.
Hand based degreasing of parts is very labour intensive.
Water-based cleaning can be carried out in different ways:
- alkali based
- alkali based electrolytic or ultrasonic
- neutral
- acid
- by emulsion cleaning.
Some of these methods are described in the section dealing with electrolytic techniques. Before application of an organic coating alkali based cleaning agents are most often used.
Alkali cleaning
Water based cleaning agents mostly have complex compositions. The composition has to take into account the nature of the dirt to be removed, the cleaning method, subsequent treatments and of course the composition of the material to be cleaned. Alkali based agents often are not complex: alkali is used, e.g. a solution of Na O H, or a solution of trisodium phosphate.
In other cases complex cleaning agents are used, which consist of 3 or 4 salts, called ‘builders’, as well as a number of organic additives, such as surfactants, and complexing agents. Experience and specialist knowledge is needed for the design of such formulations.
Not only the composition of alkali cleaning agents is important, but also the way they are used. An old rule is: above a cleaning temperature of 40oC, each increase of temperature by 10 degrees will increase the cleaning effectiveness twofold. For instance at 60oC the cleaning effectiveness is fourfold compared to that at 40oC. This rule is applicable for many cleaning agents.
So, when cleaning is not very fast or effective, one should clean at a higher temperature.
In household applications of soap and cleaning agents, agitation is a well-known method to make the cleaning more effective and faster.
Agitation can be done in a number of ways:
- rubbing
- brushing
- spraying
- vibrating (ultrasonic cleaning)
- gas development (electrolytic cleaning)
The purpose of agitation is to allow the cleaning agent with its high surface tension to perpetrate under the dirt and loosen it from the substrate.
Pickling
This is used to remove layers which can not be removed by degreasing. For instance oxide layers which have been formed during soldering, welding, heat treatment, etc. Generally, solutions of acids like hydrogen chloride, sulfuric acid and phosphorus acid are used for pickling. Aluminium is pickled and cleaned in sodium hydroxide and/or nitric acid
Conversion layers
Conversion layers are used to enhance the adhesion and corrosion resistance of organic coatings. Well-known conversion layers are phosphates on steel or iron, chromate on zinc and aluminium and anodising layers on aluminium.
There are two chromate processes: yellow and green chromate. Both processes give advanced, corrosion resistant conversion layers with good adhesion properties for a top organic coating. In electronic products chromate layers are applied on aluminium to ensure a good contact resistance.
Cr111 solutions are being developed for the replacement of chromate (Cr VI) layers.
In many cases conversion layers are used as an end treatment, without an organic top layer. Anodising layers are often used (see the section on Anodising). Chromate layers on zinc are used as a top layer for corrosion resistance (see the section on Electrolytic zinc), also used on aluminium, as a top layer for the realisation of special electrotechnical applications. A special treatment is needed for good adhesion of organic coatings on aluminium. Chromating is used for this. Phosphate layers are used as a lubricant layer during deep drawing of steel plate and as top layer on e.g. barrels of shotguns and pistols.
Cr VI containing conversion layers have drawbacks from environmental and health points of view. Alternatives are anodising, zirconising and titanising.
An organic coating system, consisting of a chromate (yellow), primer (white) and top coat (blue).
Properties
Yellow chromate: the colour depends on the coating thickness and varies from colourless to yellow.
Normally a light yellow chromate is applied with a mass of 0.4 to 0.8 g/m2.
The layer mainly consists of basic chromiumchromate.
If covered by an organic coating, these layers can be stoved at maximum 240°C (object temperature). Thick layers are mechanically weak.
Uncovered chromate layers will crack above about 70oC. Small cracks in the chromate layer will decrease the corrosion resistance.
Green chromate is less sensitive than yellow to impurities such as phosphate and sulphate.
Chromate layers have a good flexibility.
Zirconium and titanium layers are very thin (about 10 nm), consisting of complex Zr-Al or Ti-Al layers.
Applications
Chromate layers or Ti- or Zr-layers are especially used to obtain a good adhesion of wet or powder coatings on aluminium. This pretreatment is especially necessary for aluminium that is used outside in the atmosphere. Chromate layers are applied on aluminium to ensure contact resistance. This is important for radio, TV and electronic applications.
Aluminium building profiles are chromated or zirconised prior to organic coating
Substrate
Chromating is mainly applied on aluminium. A similar process is used as an after - treatment on electrolytic zinc ("passivation"). A strong increase in corrosion resistance is obtained in this way.
Conditions
Conversion coatings on Al can be obtained by spraying or by immersion in a bath. Maximum dimensions of parts depend on the bath dimensions.
The process
During the process, aluminium is dissolved in the bath, and H2 gas is developed because the hexavalent chromium reduces to a trivalent chrome compound. The H2 development at the surface will shift the degree of acidity (pH) from acid to alkali so that the trivalent chromium will deposit as chromiumchromate.
Specially added accelerators ensure a reproducible layer growth. The chromate layers can be de - coloured by dipping them in warm water before drying. The disadvantage of this is that part of the corrosion resistance is lost.
Examples
- A process series for yellow chromate
- Degreasing
- Rinsing
- Etching with acid
- Rinsing
- Chromate formation
Micrograph of a green chromate layer on aluminium. This layer does not contain hexavalent chromium.
A process series for aluminium-zirconium complex:
- degreasing
- rinsing
- etching
- rinsing
- demi-water rinsing
Chromating is carried out by immersion or spraying of the chromate solution over the aluminium surface. Titanising or zirconising is carried out in a similar way.
After treatment the product is rinsed in very clean demineralised water followed by drying at max. 65oC object temperature.
Advantages and disadvantages
Chromate layers offer an active corrosion protection since small defects in the layer are restored automatically. An explanation for this is that chromium acid dissolves in the surface film as well as the aluminium, resulting in the formation of alkali chromiumchromate.
A disadvantage of chromate layers is their toxicity.
A disadvantage of titanate or zirconate layers is that they only have a barrier function and not an active corrosion protection. The advantage is that they are not toxic and have no environmental drawbacks.
The cost of all these treatments is low.
Phosphating
Phosphating is a process that is similar to chromating. Often rust is formed under a paint layer on steel. This results in bubbles and the detachment of the layer (under-rust). Under-rust formation is prevented or slowed down by application of a phosphate layer, formed by conversion of initially present iron oxide / hydroxide.
We see that there are 2 main reasons to apply a phosphate layer before painting:
- adhesion improvement
- prevention of under-rust
Phosphating of steel may also be applied for several other reasons. A phosphate layer has electrically insulating properties. For this reason transformer plate is phosphated. The core of an electrical transformer is formed by a series of thin steel plates to avoid electrical losses. The individual plates are insulated from each other.
Steel plate is phosphated before painting; in this case zinc phosphate is formed.
Another application is in sliding machine parts, such as parts of seals, fire-arms and engines. The thick phosphate layers which are used here can take up some oil, resulting in a lubricating function. These oil containing layers are also corrosion resistant.
In the cold forming of steel, such as in wire drawing, deep drawing of steel plate and cold forging, the steel is phosphated, since this lowers the friction, so that a higher deformation can be reached, without damaging the material. A better surface finish is also obtained.
The process of phosphating
An acid salt is a compound in which not all hydrogen atoms of the salt have been replaced by metal atoms. Phosphoric acid has three hydrogen atoms in each molecule, so that different acid salts can be formed:
- Na H2 P O4 mono sodium phosphate or primary sodium phosphate, one H-atom replaced by Na
- Na2 H P O4, di sodium phosphate or secondary sodium phosphate, two H-atoms replaced by Na
- Na3 P O4, tri sodium phosphate, all three H-atoms replaced.
Phosphoric acid gives primary, secondary and tertiary phosphates with other metals, too. For industrial phosphating, iron, zinc and manganese are especially significant.
Micrograph of the surface of a zinc phosphate layer on steel.
|
|
Micrograph of the surface of a zinc phosphate layer on steel. The phosphate layer contains Ni, its formation was accelerated with nitrite. |
Micrograph of the surface of an iron phosphate layer on steel. |
Organic deposition techniques
Wet Painting
Introduction
The deposition of organic layers is one of the most important surface treatments.
Organic coatings can be applied as:
- foil or tape
- paint (coating constituents in a solution)
- powder
|
|
A foil is rolled on electrolytic zinc plated steel which was first coated with glue
|
Machine components coated with wet paint
|
Radiators are often coated with cataphoretic paint.
A paint system consists of a pre-treatment plus the subsequent organic coating.
Pre-treatment line. In most cases the material needs to be pre-treated before coating
Properties
Organic coatings can be made with very diverse properties. They can be very smooth and dirt repelling (esp. fluorine containing coatings such as the well known Teflon layers), rough, as on stairs and the decking of a bridge.
Some examples of important properties or functions of these coatings:
- corrosion resistance
- decoration
- recognition and camouflage
- fire resistant
- heat regulation (white colours)
- electrical and heat isolation
- light emitting properties
Compared to metallic coatings, organic coatings are relatively soft and flexible, so that product scan be partly deformed without peeling off of the coating.
Some organic coatings are highly deformable, and suitable for use in the coilcoat industry, such as on profiles for for sheet pile walls.
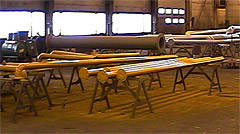 |
|
Deformation of electrolytic zinc plated and then painted profiles for for sheet pile walls. Such plates are often used on outside walls of buildings. |
Process characteristics
Paint production
Most organic coatings are applied in a more or less liquid form, i.e. paint.
The most important constituents of paint and natural additives:
- binding agent based on natural oils and resins and/or synthetic products derived from natural oils
- pigment
- solvent and dilution agents
The binding agent ‘binds’ the paint and all its constituents and adds to the adhesion on the substrate.
The pigment primarily delivers the colour and coverage. The pigment can have other functions, such as corrosion protection. Lacquer or varnish is paint with binding agent, but without pigment.
Solvent and dilution agents are used to make the paint processable. They only serve once, namely during the application of the paint. After application they should disappear as soon as possible.
There are solvent-free paints, based on liquid binding agents, and powder paints which are also solvent-free.
Generally, the industry strives to use less organic solvents, in view of their possible harm for man and environment. Water-based paints are being introduced, rapidly.
Varnishes
Varnishes are paints without pigment, also called white paints. There are also paints without binding agents, e.g. in cosmetics.
Next to these three main constituents, other constituents are used in paint, for conservation, processing, film formation and functionality during use:
- anti-sagging agents
- anti-skin agents
- thixotropic agents
- anti-hazing agents
- drying agents
- anti-scratch agents
Film formation
Depending on the type of binding agent, there are different film formation mechanisms. Film formation is the growth of the film out of the different constituents in the paint. Important mechanisms of film formation are:
Polymerization, physical film formation, and chemical film formation.
Summary
Polymerisation is the forming of macromolecules from much smaller molecules of the monomer.
Poly-addition (only growing together)
Homopolymerisation (one kind of monomer)
Hetero polymerisation (more than one kind of monomer)
Poly-condensation (one small molecule is released)
Most paint binding agents are already polymers.
Physical film formation
Only physical processes
Evaporation (reversible)
Coagulation (irreversible)
Gel formation (irreversible)
Solidification (reversible)
Chemical film formation
Oxidative drying
Film formation in two-component paints
Film formation in stove enamels
Chemical film formation is never reversible.
Physical film formation
Evaporation
Coagulation
Gelation
Plastisols
Organosols
Solidification
Bitumen
Hot-melt plastics
Thermoplastic powder coatings
Chemical film formation
Oxidative drying
Film formation of two-component paints
Stoving
Note: Chemical film formation is often preceded by or takes part together with evaporation of solvent and dilution agent.
Polymerisation
Polymerisation is a general concept, encompassing different ways in which smaller molecules link, to form bigger ones.
One can distinguish:
- poly-addition
- homo-polymerisation (one kind of monomer)
- hetero-polymerisation (more kinds of monomer)
Poly-condensation
In poly-addition, molecules grow together without separation, whereas in poly-condensation a small molecule such as water or formaldehyde separates.
These two types of polymerization are found with enamelling and with two-component painting. In two-component painting, the hardening agent may cause “cross - linking", where connections are formed between long molecules.
Many binders in paint are polymers. This is the case with nearly all physically drying (by evaporation) paints. Also in chemically drying paints polymers are often used as starting material for the binding agents, which then in further reactions grow together into larger units, so that the dried paint can be considered as one macromolecule. Also mixed systems exist.
Physical film formation
In physical film formation, the paint is exclusively formed by physical processes, such as evaporation of the solvent. No chemical changes take place in the binding agent. The molecules of the binding agent in the liquid paint and the dried paint are of the same size. Physical film formation by evaporation has been the most important way of paint formation for a long time. Now other film formation processes have been added.
Film formation by evaporation
Binding agent molecules are mostly elongated. They exhibit a strong mutual binding which can be broken by the much smaller molecules of a suitable solvent. In solution the binding agent molecules can move freely. The less solvent, the larger the interaction between the binding agent molecules, and the higher the viscosity of the solution. Solvents liquefy the paint.
Pigment grains form a large part of the paint. During evaporation the solvent and dilution molecules disappear, the paint film gets more viscous. The influence of the pigment then increases, the liquidity decreases.
Finally, at the end of evaporation, no movement is possible between the binding agent molecules and the liquid film has transformed into a solid state. It is may be that residual solvent or dilution agents are present in the film, but not in a quantity which enables movement of the molecules. This means that after drying the properties of the film are not optimal. After a certain time the last remains of solvent or dilution agents will have diffused to the surface of the film and evaporate. Only then the film has its final properties.
As soon as a proper solvent is added to a dried paint film, the reverse process will take place. The solvent molecules will push themselves between the binding agent molecules, these can move again, and the film regains its liquid state.
A dry paint film can always dissolve in its own solvent, the process is reversible.
Well known reversible paints are cellulose paints, chlorine rubber paints, bitumen paints and shellac varnish.
When paint is not soluble in its own solvent it is called irreversible. Irreversible paints are found with physically drying paints and with chemically drying paints.
Film formation by coagulation
Coagulation is a phenomenon during film formation of emulsion paints. Emulsion paints consist of droplets, floating in water, and containing half liquid pigment and binding agent molecules (In NAD paints there is no water, but organic solvent). The water contains the emulsifier which stabilises the emulsion.
Emulsion paint is made by intensively mixing a complete, thick paint with water. This causes the (small) paint droplets to distribute uniformly in the water.
The emulsifier prevents merging of the paint droplets. When the water evaporates, the emulsifier is not active anymore. The separation of the paint droplet stops and the emulsion ‘breaks up’, causing the half-liquid droplets to merge and form a uniform paint film.
The different phases of film formation for emulsion paint are clearly visible in wall paint. Direct after applying the paint, the film is lusterless. At that moment the paint is removable with water.
After some time shining spots appear in the film. The water has evaporated and the paint droplets are merging and forming a shiny film. In this stage it is difficult or impossible to remove the paint with water. The film however still contains a certain amount of solvent and water.
After complete drying the film is again lusterless (depending on composition). Then the paint cannot be removed by water. It is then washable; it can be cleaned with water.
It should be noted that there are emulsion paints which contain reactive groups which cause the paint to harden during film formation, by temperature increase (stoving) or at room temperature.
Film formation by gelation
Gelation is the process where a solvent with a suitable gelation agent gets stiff, and transforms into a gel. Well-known examples are jelly or jam.
In paint technology this is applied in another way. A very finely distributed synthetic resin, e.g. vinyl resin is used, in the form of a pearl polymer (very fine and hard resin particles).
This resin powder is mixed with pigment in a suitable softening agent into a thick paint mixture. At room temperature the softening agent does not influence the resin particles. At elevated temperature, however, the softening agent penetrates into the resin particles and causes these to swell. They will touch each other and merge.
Then a thick uniform paint film has formed, without removal of a component of the paint. In this way, thick films are applied which are ductile and behave similarly to rubber. These layers are called plastisols. They can be applied as thick layers up to a few hundred micrometers.
If a certain amount of organic solvent is also added the mixture can be sprayed. Normally these layers, which are called organosols, dry by evaporation at elevated temperatures. They are thiner than plastisols.
Film formation by solidification
Film formation by solidification from a liquid phase takes place in bitumen. Also the so-called hot-melt plastics and thermoplastic powder coatings exhibit this film formation mechanism.
Since the solidified layer can be made liquid again by heating this is a reversible process too. Of the physical film formation processes only film formation by evaporation and by solidification are reversible.
Chemical film formation
In chemical film formation a chemical reaction takes place in which the binding agent is involved, and which causes the solidification. Only in a small number of cases only chemical film formation takes place. In the majority of cases also evaporation of solvent and diluting agent takes place. In chemical film formation the binding agent molecules, often polymers by themselves, grow together into larger units, so that finally the whole paint can be considered as a huge macromolecule.
Oxidative drying
Oxidative film formation or oxidative drying takes place with oil containing binding agents. These are binding agents used in oil paints and in (oil containing) alkyd paints.
In oxidative drying oxygen bridges are formed between the unsaturated fatty acid chains of the drying oils used in these binding agents.
Film formation in two-component paints
Commonly, for two-component paints the two components of the binding agent are mixed prior to use, after which film formation and solidification take place by a chemical reaction between the two components.
In epoxy paints the basic paint contains a polymer, the epoxy resin which has not yet hardened. The hardening agent often is a polymer too, an amine-adduct (free amines are seldom used), a polyamide, polyamino-amide or isocyanate. As a rule, the reaction takes place at room temperature. Some two-component epoxy paints are stoved in order to obtain optimum properties.
In epoxy powder coatings the hardening agent is mixed with the base paint by melting and then ‘frozen together’ by rapid cooling. By then some hardening has already taken place. Only upon heating does complete solidification reaction take place.
In isocyanate paints the hardening agent can be a complex and large molecule, but it can also be simple, such as water, e.g. in the water hardening PUR paints. Many isocyanate paints completely harden at room temperature.
Sometimes the hardening agent is blocked or masked (with caprolactam). The hardening molecules are only set free upon heating and then cause the solidification. These paints need to be stoved.
At elevated temperature the caprolactam disappears by evaporation.
With some polyester paints, the base paint and hardening agent are already present in the paint. Some additions prevent their reaction. One could say “they are on the handbrake”. By adding a catalyst, most often an oxidation agent, the reaction quickly starts.
Film formation of stove enamels
Stove enamels can contain very different binding agents, so that different reaction mechanisms can take place, for instance the hardening reactions of amino-alkyd paints, the most common stove enamels based on urea, melamine or HMMM.
In fact these are oxidative drying paints, with other hardening agents added. The following reaction mechanisms may take place:
- oxidative drying of the oil component
- formation of oxygen-free bridges in the oil component
- poly-addition of added components
- to a certain degree also poly-condensation.
Which mechanism is the most important, determines the paint properties. For instance, oxidative drying gives a more flexible product than other hardening mechanisms by the formation of oxygen bridges between flexible oil fatty acids. Which hardening mechanism takes place depends on the stoving temperature and time.
For this reason it is important to follow closely the prescriptions of the paint producer. Thirty minutes stoving at 140°C may not be changed into 5 minutes at 190°C. The paint layer may still have a good appearance, but the durability is inferior.
Pretreatment of car gas tanks before painting
Overview of application methods
The application of a powder is described in the section on powder coating.
After, or sometimes during application, the layer should be transformed into a coating with the desired properties.
This can be done by:
Drying
Flowing together
Hardening
Combinations of these are often applied. Physical and chemical processes may appear together or following each other.
The following application methods are common:
Use of brush or roller
Spraying
Paint rolling
Dipping, casting or application in a paint barrel
Screen printing
Application with a broom or scrubbing brush
In spite of the high labour costs the paint brush method has a number of advantages as compared to the broom method. One is the intensive contact with the substrate, which gives complete coverage of lower lying parts of a rough surface. Another clear advantage is the negligible loss of paint. No other paint method has such a low paint loss.
The low production speed is an advantage too, because defects are easily spotted and repaired. Dust can be mixed with the paint during brushing and is less harmful than during spraying a uniform layer. In such a case a weak spot may be formed.
Rolling
By using rollers the application can be faster than with an ordinary brush.
Spraying
Important spraying methods are:
Pneumatic spraying
Airless spraying
Electrostatic spraying
Consumer products coated with a wet paint system
Pneumatic spraying
Conventional air spraying is the oldest spraying method. This method was introduced in the 1920’s and is still the most common one.
Conventional air spraying has two main advantages as compared to other methods:
Control
The highest degree of control can be obtained with this method. The spraying operator can influence and optimise the results, if properly trained. This method can give the finest dispersion.
Applicability
The largest variety of coating systems can be applied with this method. It is easy to use and maintain, and lots of expertise and equipment are available.
An important disadvantage of conventional air spraying is the large overspray, i.e. the paint which is taken by the air and is not applied on the product. Often the overspray is 40 to 50% of the total paint volume. Newer types of spray guns, the high yield guns, significantly limit the overspray by a better air pressure distribution and optimized nozzle. In the automobile sector these guns are compulsory.
The paint cloud can be clearly seen. The cloud is considerably smaller than with conventional pneumatic spraying.
Airless spraying (high pressure spraying)
In the sixties of the last century, another method of paint spraying has been introduced, now known as airless. In airless spraying no pressure air is used to spray the paint. Instead, hydraulic pressure is doing this, by pumping the paint up to high pressure (3.5 to 31 Mpa) through a nozzle with a small diameter hole (0.18 to 1.8 mm). The high pressure causes the paint to atomize upon leaving the nozzle. As a result of the high speed during atomizing sufficient impulse (mass times speed) is left for the paint to reach the object. It is important to determine the maximum spraying (spray width) angle and the smallest nozzle opening before spraying.
Airless spraying has four distinct advantages:
High working speed
Less recoil of the paint spray
The paint will reach notches and holes with only limited recoil
Less maintenance of the spray cabin needed.
The high working speed is due to the following factors:
The high volume of displaced paint
The high viscosity of the paint (higher layer thickness in one time).
The limitations of airless spraying are:
Coarse spraying process
Less control over the spray pattern
In order to prevent drops in the paint layer it is necessary to work with great care, and to regularly maintain the nozzles and pumps.
The high paint pressure is potentially dangerous: the paint jet near the nozzle can cause injuries.
In the beginning, airless spraying was used on large surfaces, with lower decorative requirements.
Typical examples were the ship building and steel constructions. For these applications airless spraying is still the most important application method. But the technique is now used in a wider range of applications, e.g. in equipment building. Here too the advantages of high working speed and thicker layers in one run are important.
Construction steel is sprayed airless. In view of the variety in shapes, weight and dimensions of the parts it is not always possible to hang these during spraying. Consequently, these parts are sprayed on the floor.
Electrostatic spraying
In electrostatic spraying the paint droplets are given a high electrical charge. All droplets are charged in the same way when they leave the gun.
The parts to be painted have the opposite charge (by induction), so that the paint droplets are drawn to the parts.
|
|
Electrostatic spray equipment |
Cleaning by hand |
Not only electrical forces influence the paint droplets, also gravity and the air ventilation in the spray cabin play a role. Also, the droplets have a certain speed upon leaving the gun.
The final trajectory of the droplets results from all these forces. Since the trajectories are curved, even the back side of objects (as long as these are not too wide, can be covered.
The tubes of a bicycle frame are coated in this way.
Also aluminium profiles are excellently suited to be sprayed electrostatically.
Steel cases etc are coated with wet paint. The main aim of electrostatic spraying is to minimize paint losses.
Pneumatic spraying: about 50% loss
Airless spraying: about 25% loss
Electrostatic spraying: about 15% loss.
Immersion
Immersion techniques are often used in industrial fabrication.
Immersion technique
Immersion of parts in a paint bath should be done in such a way that hollow parts cannot form air pockets. It is advised to turn the object during immersion so that air inclusions can disappear.
It is important to test which speed is optimal to immerse the object. If the speed too high, then air bubbles may be formed at the surface. Of course this also depends on the roughness of the object surface. Air bubbles may cause defects in the paint layer when the object is removed from the paint bath.
During removal from the immersion bath care should be taken that no pockets of liquid paint remain. The paint should flow off as regularly as possible. After immersion, the painted object is hardened in an oven. One particular variant of immersion is electrocoating.
Electrocoating (electrophoretic painting)
Electrocoating, also called electrophoretic painting, is an important technique, especially since it is being applied on a large scale in the automotive industry.
After zinc phosphating an immersion paint is applied, in this case a cataphoretic paint.
During electrocoating, paints are used of which the binding agent is water - soluble. In solution the particles of the binding agent are relatively large, they are colloidal particles or micelles, which are weakly charged. This charge allows them to move in an electric field (electrophoresis). After discharging at the electrode, the paint particles will merge and form a insoluble (in water) paint layer. Apart from binding agent particles, also pigment particles and ions (much smaller than the binding agent particles) are present in the water soluble paint.
Between the object and the bath wall an electrical potential is applied, and as a result of the resulting electrical field, the paint and pigment particles will move towards the object.
When the paint layer is deposited on the object’s surface (after discharging) the layer is already hard enough for the object to be removed from the immersion bath and rinsed.
During cataphoretic painting in principle a good uniformity of the paint can be obtained. The paint layer itself is an insulator, so that after some time the current will move to holes in the object where no paint has been deposited. Electrocoating is also used in electroplating on zinc and nickel layers, to enhance their corrosion resistance.
Anaphoresis and Cataphoresis
During anaphoresis the binding agent particles are negatively charged. Under influence of the voltage difference the particles are drawn to the anode i.e. we have anaphoretic painting.
In order to disperse the binding agents chemicals are needed which provide ammonium- or amine - ions. Anaphoretic paints are for instance used on aluminium.
In cataphoretic painting the binding agent is coupled to the cation of the acid. This method, where the objects are coupled to the cathode, is generally used in the automotive industry. It avoids corrosion of the substrate steel.
Paint rolling
Paint rolling or coil coating is an automatic deposition technique, mainly used during production of semi - finished products.
During coil coating rolls of metal, e.g. steel, galvanized steel or aluminium are pretreated, painted and stoved in large installations in a continuous process.
|
|
A coil coat installation |
A coil is a roll of metal, often steel, aluminium or brass. |
These installations include sections for cleaning and pretreatment, paint application and stoving.
The rolls of metal are gradually unwound. The installation contains an accumulator, e.g. a section where coil material is saved in case the roll has to be replaced. A short stop is then needed, but the installation can continue at normal speed while using material from the accumulator.
The old and new coil are welded together. Similarly at the end of the installation there is an accumulator which allows for continuity in production, while a roll is replaced. Characteristic for a coil coat installation is the application of the paint. This is done by rolling, on one side of the coil, or on both sides. The rollers turn either in the same direction as the coil (forward roller coating) or against the coil direction (reverse roller coating). In some cases, other application methods, such as electrostatic spraying or paint casting is used for continuous coating of coils.
Foil rolling
In continuous systems steel, galvanized steel or aluminium coils can be coated with a foil which is glued to the coil surface. The glue is hardened immediately after painting. Well known foils are PVC and PVF (Teflon).
Spraying
Several spraying methods are used for paint application, both manually, and in a machine. The most important are
spraying with a hose
spraying with a spray gun
spraying with paint curtain machines
Paint curtain machines
Paint curtain machines are special spraying machines for paint. This machine is equipped with a shallow, vertical slit, through which the paint film is pumped.
Sieve printing – screening or screen printing
Complex texts and drawings can be produced on a substrate material by sieve printing or screening.
Examples of sieve printing
In screen printing a sieve of a fine mesh fabric is used, consisting of metal, nylon, silk or other material. The sieve is covered by a gel layer which is not fully hardened. This gel contains a species which can harden the layer and make it insoluble when subject to light, preferably UV radiation.
A model of the text or drawing which should be transferred is now placed on the sieve. Then the sieve is illuminated, after which the uncovered parts are insoluble. The covered part can be washed away by water. In this way the sieve is ‘printed’ with the image. For screen printing paints are usually used, but also special enamel pastes are possible, which are applied and pushed through the mesh by a doctor blade.
Sieves are characterized by the number of strands per cm2 and the filament thickness. The filament thickness also determines the screen thickness, since two times the filament thickness equals the sieve thickness. The more filaments per cm2 the finer the screen and the more uniform the pressure. A drawback of fine-mesh sieves is that they are susceptible to damage.
Screen printing is often used in electroplating, e.g. in the precision etching and fabrication of printed circuit boards. Also in anodising it is used for the reproduction of images or texts in the anodised layer.
A variant is tampon printing where a kind of stamp is used to apply signs or marks on the painted component.
Tampon printing is used to apply signs or marks on a painted component
Advantages and disadvantages
Advantages
Organic coatings have many advantages compared to other coatings:
- they can be applied on any material, e.g. metal, ceramic, wood or glass
- any colour or lustre is possible
- by varying the formulation of an organic coating almost any property can be realised.
Disadvantages/limitations
A limitation is that an organic layer is generally less hard and wear resistant than a metallic or an inorganic layer.
Cost
Cost is depending on the necessary pre-treatment, the method of application, and the type of paint chosen. Typical cost is in the range of € 2 to € 15/m2.
Application
The application possibilities of wet painting are very large:
- protection against corrosion: cars, ships, steel constructions, etc.
- for decoration: appliances, cars, bicycles, chairs, etc
- insulation, e.g. of wire
- camouflage: less precious objects such as silos, and in military applications
- strengthening: paper, lamp of a bike, tabletops, surfaces of artificial leather, etc.
- temperature regulation: tankers, storage tanks, etc.
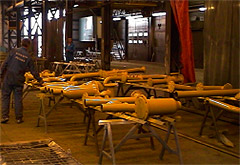 |
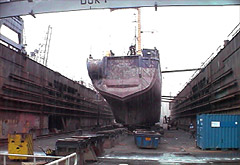 |
Construction steel: after pretreatment, in this case by grit blasting, a wet painting is applied by airless spraying |
Sea ships are painted in a special dock. A water shield is used to prevent the wet paint from polluting the surroundings
|
|
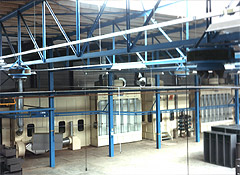 |
Wet paint installation for steel frames |
Steel furniture in a wet paint installation |
- cleaning: anti-burning layers, anti-graffiti, etc.
- colours for signaling: recognising pipes, fire protection material, etc.
- making a surface rougher: on stairs, ship decks, etc.
- prevention of fouling on ships
- lubrication, e.g. self-lubricating paints
There are numerous other applications. In order to fulfill the requirements of each application, many different organic coatings have been formulated, with many different properties.
|
|
Appliances are often coated with a wet paint or powder paint |
Construction steel |
Conditions
Depending on the type of wet paint there are less or more conditions. Stove enamels are hardened in an oven. The objects obviously cannot be larger than the oven, and the substrate should be suitable for stoving the enamel.
Two-component coatings may require a minimum temperature for application, e.g. not lower than 4 °C.
Organic coatings are so variable that almost always a composition can be found which fits the requirements.
Organic deposition techniques
Powder Painting
Introduction
The electrostatic or electrokinetic deposition of a thermohardening organic powder on a metal. After hardening in a furnace, a strong and tough powder coating is formed, - good corrosion and chemical resistance.
|
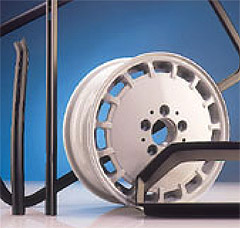 |
Modern office building with powder coated aluminium façade |
Car parts |
|
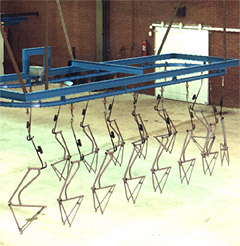 |
For in-house walls often powder coatings are used |
Powder coated bikes |
|
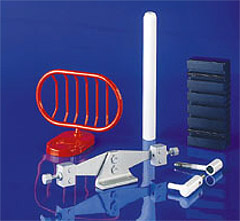 |
Powder residues after cleaning a powder spray cabin |
Since there are different powder coat compositions, with differing properties, it is possible to select the optimum coating for each application. |
There are different powder coat compositions, with differing properties. Thermohardening powders can be applied by cyclone sintering. Usually cyclone sintering is used for all thermoplastic powders.
Properties
Thermohardening epoxy powder coatings can have different properties. The most important are:
- a good chemical and corrosion resistance
- degrees of brightness can be chosen
- by applying catalytic hardeners, coatings can harden at lower temperatures and are readily repaintable
- not UV resistant
Many powder coat companies have a laboratory for measuring the mechanical properties of coatings.
Thermohardening polyester powder coatings. The most important properties are:
- special appearance
- degrees of brightness are possible
- strong and flexible coatings with a good mechanical load bearing capacity
Office building with powder coated façade parts
Thermohardening polyester-epoxy powder coatings. The most important properties are:
- special appearance
- degrees of brightness are possible
- strong and flexible coatings with a good mechanical load bearing capacity
Aluminium profiles are powder coated in many different colours and degrees of brightness.
Substrate e
Epoxy: can be used on almost all metal substrates, most prominent are steel, galvanized steel and aluminium. Also several plastics can be powder coated.
Polyester: can be used on almost all metal substrates, most prominent are steel, galvanized steel and aluminium.
Epoxy-polyester: can be used on almost all metal substrates, most prominent are steel, galvanized steel and aluminium. Also glass, ceramics, plastics such as MDF and galvanic substrates can be made suitable for an epoxy-polyester powder coating.
The metal substrate is coated with a thermal zinc layer and then powder coated. This is called a duplex system.
Process characteristics
Electrostatic Powder Spraying
In Electrostatic Powder Spraying (short: EPS) thermohardening powder particles are charged using a special gun, disc or cylinder to a high potential. The charged particles will move to the zero potential object and form a uniform layer on it.
|
|
Powder spray cabin; the spray powder sticks to the objects and the coated objects are transported to the furnace.
|
These profiles are elongated at zero potential
|
As a rule the objects have been pretreated mechanically or chemically, as in phosphated steel or zinc, or chromed aluminium and zinc. This chemical pretreatment generally is much more effective and generates a much better adhesion than is the case in fluidized bed sintering. The powder particles stick to the object as a result of electrostatic forces, which enables the objects to be transported to an oven.
In stoving the following processes take place:
- the powder particles begin to melt, and stick to the substrate surface
- the electric charge flows to zero potential
- the powder particles melt and flow together to a uniform layer
- the chemical reaction with the hardening agent in the powder starts during flowing of the powder (at sufficiently high temperature); the powder reacts completely and a thermohardening layer is formed.
In this way coherent layers of good quality are formed.
An advantage of the electrostatic powder spray process is that in the beginning extra powder is deposited on edges, because edges have a higher concentration of electromagnetic field lines. This effect is partly lost as a result of the surface tension of the melt, but generally powder spray coatings are rather uniform at edges.
|
|
During electrostatic spraying the powder particles move along field lines to the object, which is at zero potential. The field lines are determined by the form of the object. Round objects are uniformly covered. The back sides of flat objects are only covered at the edges.
|
|
|
Powder spraying of aluminium profiles.
The powder cloud – which follows the field lines – can be clearly discerned. These profiles are used for the outside of buildings.
Under Fig. 5: Cross section of a two-layer system powder coating. Although powder coatings are generally applied as a one-layer system, building profiles and surfaces are often coated with a two-layer system. A two-layer system gives extra corrosion protection. The good cover at the edges can be seen clearly. |
|
|
Cross section of a 2-layer system after powder spraying; during façade building often 2-layer systems are used. These layers give a better corrosion resistance. The good coverage can be seen.
|
|
|
Since flowing and hardening of a powder coating take place simultaneously, the coating cannot spread in a perfect way. A wet paint coating therefore is more even over the surface than a powder spray coating (the orange peel surface effect). The coating thickness of layers which are deposited in one step generally is higher than with wet painting, and between 50 and 80 µm.
During hardening, no chemical substances such as solvent agents have to evaporate, as is the case for wet painting. Powder particles which are not sprayed on the objects generally land in special ventilation systems, where they are collected in sieves, cleaned, mixed with new powder, and re-used.
|
Powder spraying is a clean process. Powder coat companies therefore have clean floors.
Electrostatic powder spraying generally is more environmentally friendly than wet painting, where solvents are being used.
Fluidised bed sintering
For fluidised bed sintering thermoplastic powders such as polyamide are often used.
Fluidised bed sintering is a technique which uses fluidized polymer particles with a uniform particle size. Fluidisation takes place by putting polymer powder in a box with a double bottom, of which the upper bottom is porous, and then introducing air between the two bottoms.
The fluidised bed sintering of a spring. After heating in a furnace the spring is immersed in the flowing powder.
The air floats uniformly through the powder, so that each powder particle is surrounded by an air film. In this way the powder behaves like a liquid (a fluidised bed).
This condition can be compared to quicksand, the difference being that in quicksand the separate sand particles are surrounded by a water film. In this mass, which behaves as a liquid, pre-heated objects can be easily immersed. The heated objects cause the particles to stick and subsequently melt. When the object is removed from the fluidized bed it still looks lustre - less, but after a short time it brightens, since the polymer particles melt and flow together as a result of the heat in the substrate.
|
|
Schematics of a bath containing a fluidised bed.
The fluidized powder behaves like a liquid.
A lot of experience is needed to deposit a uniform layer on (pre-heated) complex shaped objects.
Fluidised powder
Porous plate
Pressurised air for fluidising
|
Pretreatment
Cleaning of steel, aluminium and galvanized steel is done by grit blasting and/or chemically.
For an improved chemical and corrosion resistance a conversion layer (by chromising or zinc phosphating) is recommended.
The usual pretreatment for fluidized bed sintering is to use a primer.
|
|
Pretreatment of aluminium profiles before powder coating takes place in a container where the profiles are degreased and chromised. Instead of chromising a chromate-free pretreatment is also used.
|
Layer deposition
Thermohardening epoxy powders are deposited on preheated or electrically neutral objects by electrostatic fluidized bed sintering (immersion technique) by electrostatic powder spraying.
|
|
The inside of an electrostatic powder spray cabin. The walls and floor can be cleaned easily and completely. Residual powder is quickly visible on the products after drying.
|
Schematics of the powder cycle. Powder losses are minimized by using a cyclone.
Powder centre
Filter
Container for residual powder
Cyclone
Powder pump
Powder cabin
|
|
Powder centre. Also the rest of the spray equipment, such as the powder centre, from which the powder is transported to the gun, is very thoroughly cleaned after changes of colour. |
After deposition the electrostatic powder products are cured in an oven.
During fluidized bed sintering the heat content of the pieces is not always sufficient to completely melt the particles and have them flowing together in a smooth, shining layer. Especially for thin walled pieces additional thermal treatment is necessary.
Advantages and disadvantages
Advantages:
- curing possible at different temperatures and times
- the products can be transported or used directly after curing.
Disadvantages:
- tendency to discolouring in ‘overbake’ situations
- not UV resistant, the objects become dull
- the layers are softer than e.g. electroplated layers.
Applications
Epoxy: - coating is suitable for the chemical and petrochemical industry; as primary layer in a multilayer system on grit blast and chemically treated metal substrates
- for applications in high air humidity
Polyester: - in a number of out - door applications
- on products which are mechanically loaded
Polyester-epoxy:
- for almost all inside applications
Parts of metal beds.
Conditions
A carefully cleaned substrate free of corrosion and conservation products.
Since the products have to be cured in an oven, the dimensions of this restrict the size of the objects to be coated.
Also the curing temperature can be problematic for critical parts.
| 
|
| 
|

|

|
|